infoMechatronics and Industrial Automation
Laboratory

|
|
Distributed Intelligent Control of
Modular Manufacturing Systems enabled by IEC 61499 |
The laboratory is
equipped with a range of intelligent mechatronic models forming a model
of a reconfigurable manufacturing environment, also known as Intelligent
Mechatronic Testbed.
The software control architecture is essentially decentralized.
Different hardware control architectures have been explored: from
central control to such, when each conveyor section is equipped
with its own control device, implementing its particular control
algorithm.
Some of the recent experimental projects on investigating benefits
of the decentralised intelligent control with IEC 61499 are presented
below:
|
Running very Same Software on Different Hardware Architectures |
Sample
architecture 1: EtherNet connected
IEC-61499 compliant controllers with DeviceNet links to drives. Some
controllers are one per conveyor section, some serve several sections,
but all sections have their own software (function block).
|
Sample architecture 2:
EtherNet connected IEC-61499 compliant controllers
with direct connections to drives. Each conveyor section has its own
embedded controller + drive.
|
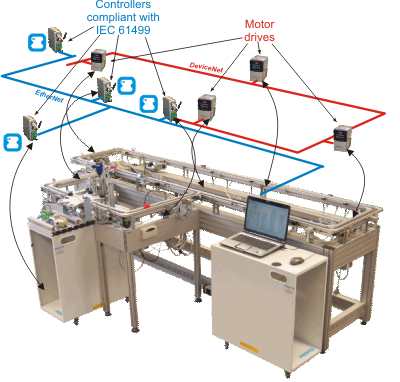 |
|
Physical Reconfiguration Experiments |
Two conveyors together form the diverting loop.
In the gap between conveyors one or two processing stations can be
inserted without any change to the control code.
|
Distributed control enables trading places of two stations “on the fly.
This and other physical reconfigurations have been achieved without
changing the code in embedded controllers.
|
|
|
Advanced Manufacturing Scenarios |
Producing different products on the same line: distributed control
adapts to the availability of mechatronic actors.
The line can keep producing some products even a machine or two are out
of order. No control change is required.
|
Batch processing plant model with distributed
control produces some
liquid product and dispenses it to the vessels on the vehicle.
The vehicle is modelled by the
Smart Pallet
with rotating table and wireless
controller.
There are several control nodes interacting as follows:
|
|
|
|
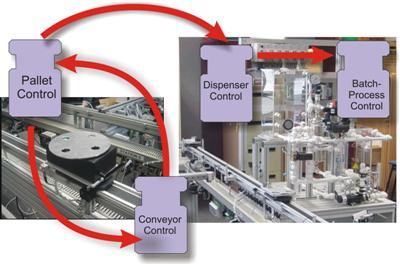
|
|
|
(C) Valeriy Vyatkin, The University of Auckland, 2007, All rights
reserved |
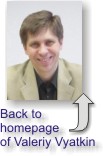 |